Infrared Paint Curing System with Long, Medium, and Short-Wave Infrared Technology (IR)
Infrared paint curing system for improved surface quality
Improve the surface quality, while reducing drying times. Surface evaporation combines with the targeted application of heat to the inside of the coating layer to effectively prevent premature surface sealing. The coating dries evenly and very quickly from the inside out. No skin or bubbles form on the surface, ensuring brilliant surface quality. Infrared technology is a suitable solution for drying coatings, particularly when the workpieces are sensitive to temperature.
Venjakob infrared paint curing systems – a future-proof investment
Our infrared curing systems are easy to access and designed to be modular. As a result, they can be configured as desired and we can fulfill your requirements to perfection. You maintain your flexibility, as Venjakob infrared paint curing systems can be retrofitted for other workpieces, materials and/or coatings in no time.
Application example
Infrared dryer in combination with other drying techniques = optimal results
But just how effective drying is it is often the result of a combination of different technologies. Tailored to your specific requirements, the concept of the individual system solution pursues the aim of ensuring optimal energy efficiency.
Specifically for Water-Based Coatings: Dryer with Optimized Infrared
For customers who use water-based coatings, we offer our in-house development, VEN DRY OIR®, which is a flat flow flash-off tunnel with optimized infrared technology.
In addition to the benefits mentioned under IR technology, Venjakob’s optimized infrared paint curing system, which is primarily used in the wood and furniture industry, also achieves outstanding results regardless of the weather thanks to the defined climate in the drying tunnel. In addition to extremely short drying times, it also boasts minimal fiber swelling and requires very little space. Needless to say, gentle energy input also reduces shrinkage cracks and bubbles in this model too, and prevents the coating film from sealing.
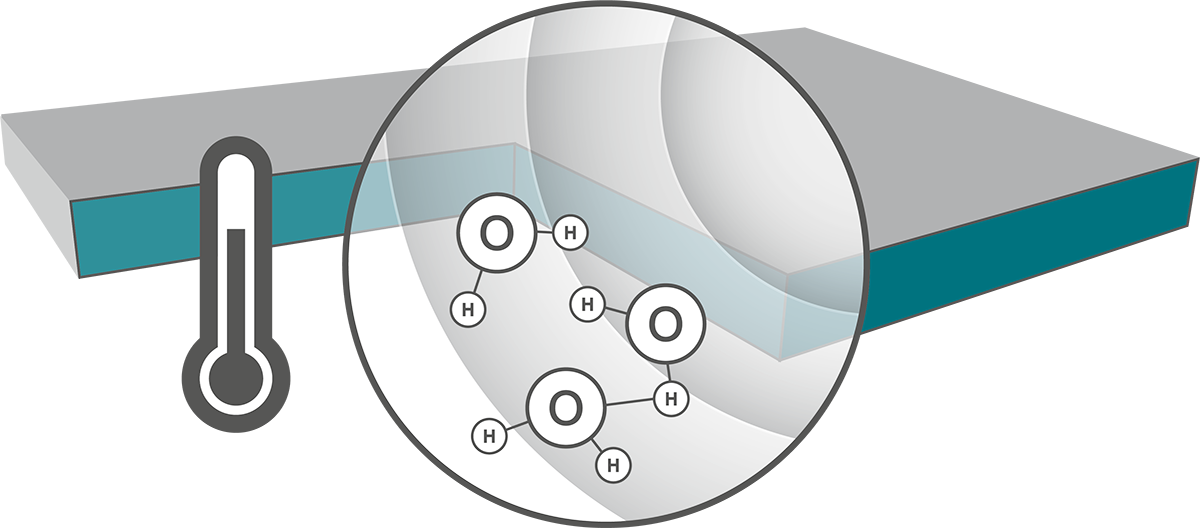
- procedure
- area of application
- advantages
procedure+
IR Technology for Preheating, Drying, and Curing
Depending on the application, the IR technology can accommodate a variety of tasks.
- Preheating: Workpieces are often heated before the coating process to improve the drying behavior of the applied coating.
- Drying: If you integrate IR technology into the circulating air oven systems, the additional energy input accelerates the drying process significantly.
- Curing: Infrared radiation (IR) improves the cross-linking of the coating.
area of application+
Applications for industrial infrared ovens
You can find Venjakob infrared curing systems in all industrial segments – as stand-alone units, integrated into production lines, or combined with other drying ovens (module).
Coating media:
- Water-based coatings and stains, dispersions
- Solvent-based coatings
- Powder coatings
Workpiece materials:
- Wood
- Plastic
- Metal
advantages+
Infrared paint curing systems are fast and efficient
Provided your production requirements allow for it, you can use infrared curing systems to accelerate your processes. Preheating workpieces in the infrared paint curing system improves the drying behavior of the applied coating and thus reduces drying times. Once the coating medium has been applied, the infrared radiation ensures optimal cross-linking of the coating and improves the curing results. There’s also no longer a need to set aside and stack workpieces to dry.
The infrared lamps used by Venjakob are highly efficient and configured precisely for the absorption spectrum, while the operating point can be adjusted for accuracy. These lamps boast a service life of well over 10,000 hours and are low-maintenance.
In coordination with you and specially tailored to your requirements, we’ll be happy to develop for you a customized concept for integrating a modern infrared paint curing system into your enhancement processes. We look forward to hearing from you!
Your contact person